Zerstören ist eine Kunst. Nur wenn wir die Belastungsgrenzen der einzelnen Komponenten kennen, können wir Laststufenschalter konstruieren, die über Jahrzehnte zuverlässig arbeiten. Deshalb zerstören unsere Ingenieure ganz bewusst kritische Teile im Test-Center in Regensburg.
MR & the art of destruction.
Motivserie von Florian Model
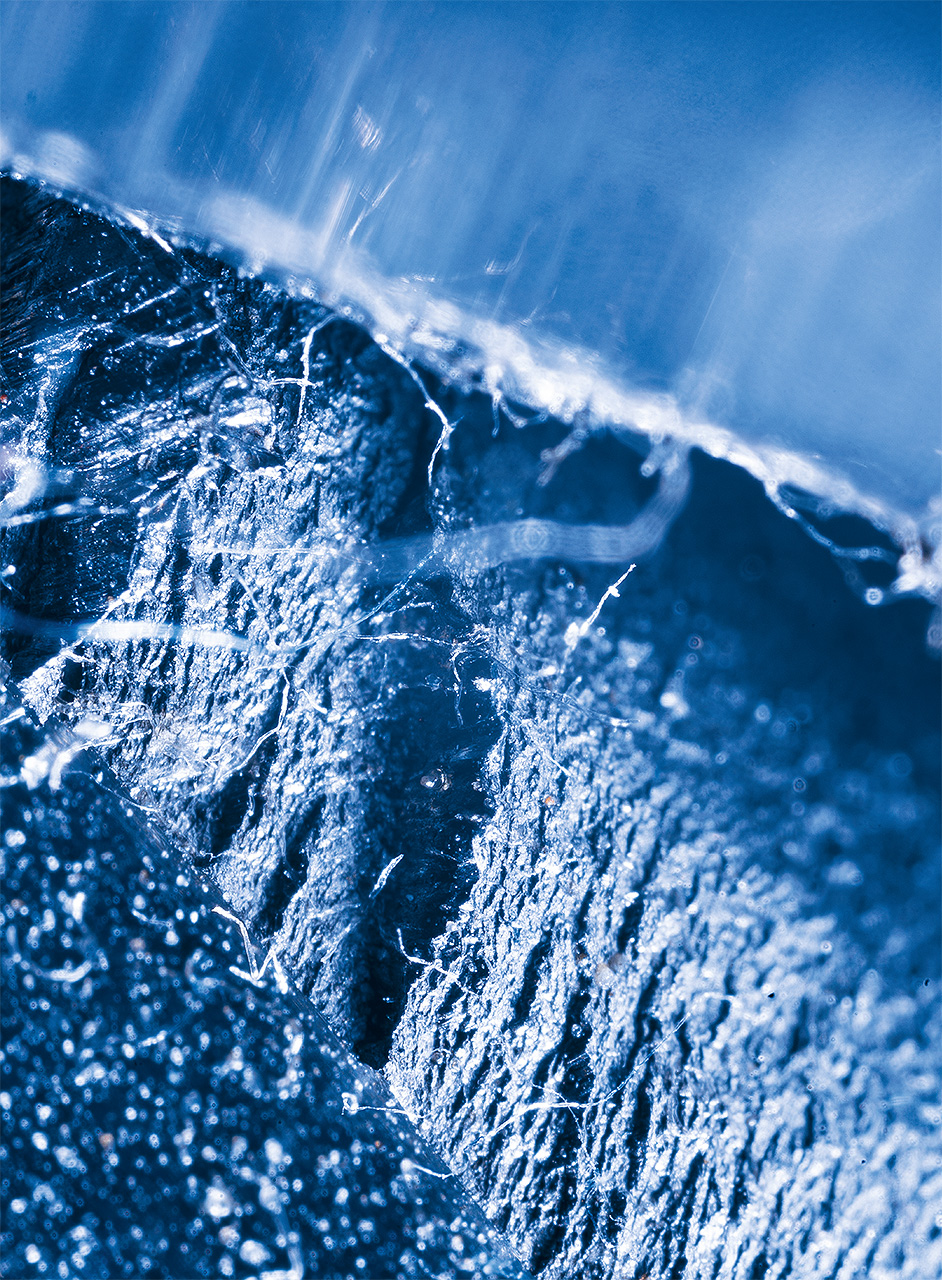

Dieses Nockenzahnrad hat einen zeitgerafften, mechanischen Schnelldauerversuch hinter sich. Bei hochdynamischer, stoßartiger Belastung wurde es bis an die mechanische Versagensgrenze geprüft. So lassen sich schon während des Entwicklungsprozesses eines Stufenschalters Schwachstellen vorzeitig identifizieren.

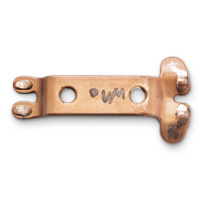
Wählerschaltkontakte müssen über die gesamte Produktlebensdauer eine sichere Kontaktierung gewährleisten. Um die Beständigkeit zu testen, wurde dieser Kontakt über 1.500.000-mal und bei Temperaturen von minus 25 bis plus 105 Grad Celsius mechanisch geschaltet.
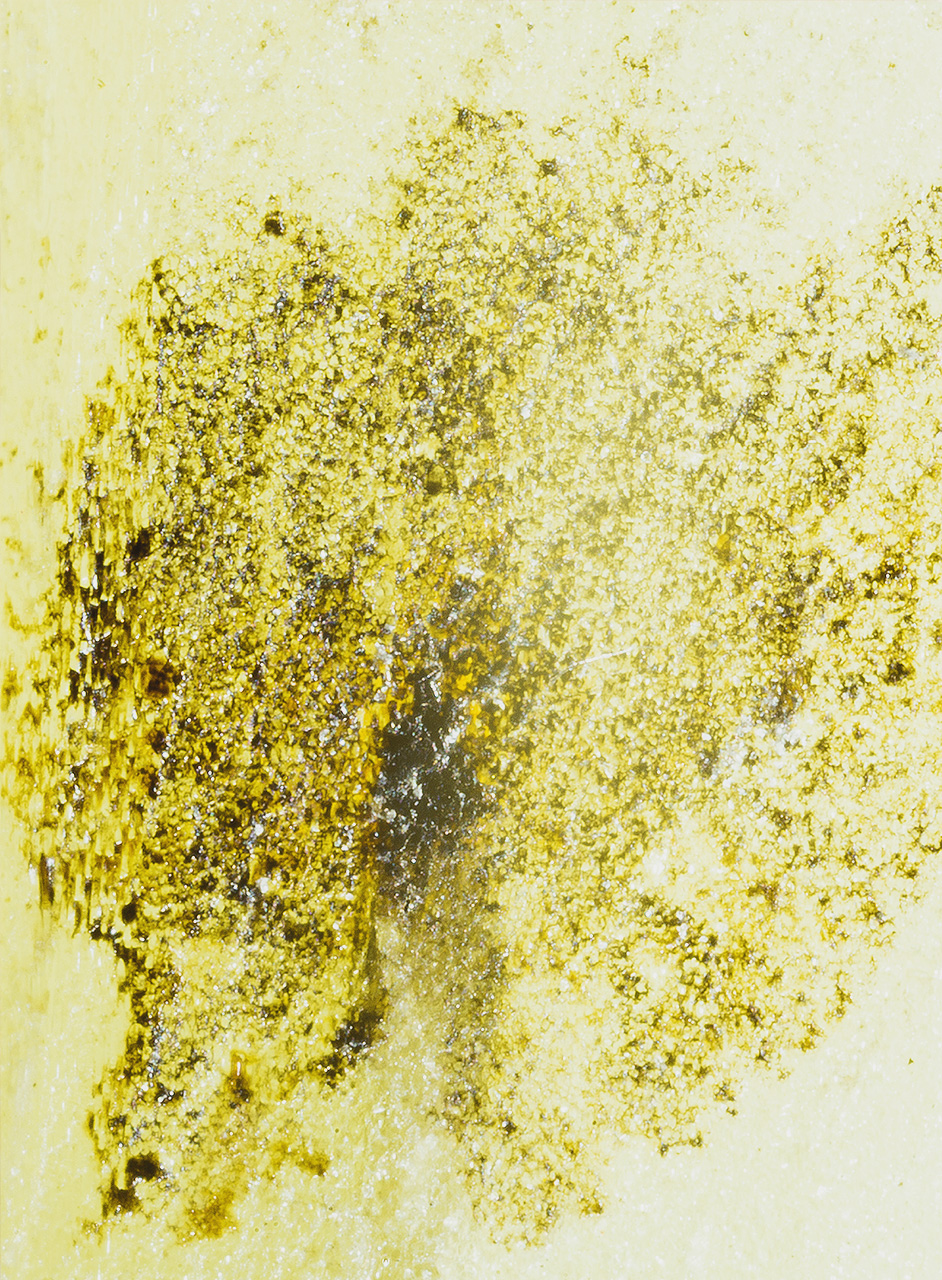
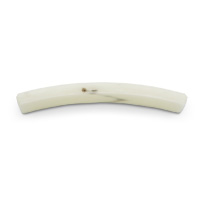
Die Materialprobe aus dem Stufenschalterölgefäß für den Lastumschalter hat in mehreren Stufen bis zu 150 Kilovolt abbekommen — so lange, bis sie versagte. Mit diesem Test lässt sich die Güte des Materials bestimmen.
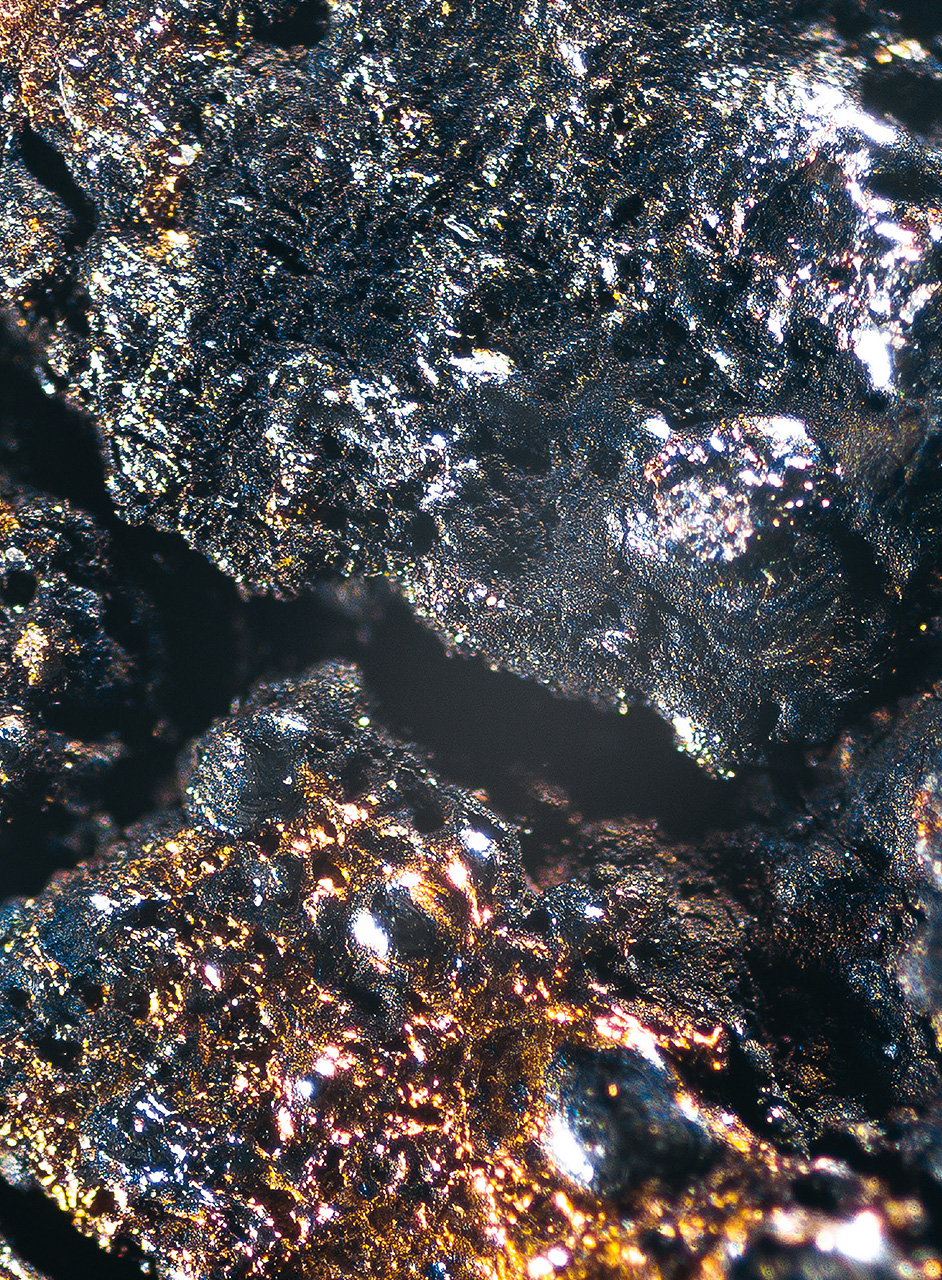

Dieser Schaltkontakt aus einer Sinterung von Wolfram und Kupfer ist für einen Maximalstrom von 350 Ampere ausgelegt. 50.000-mal wurde an dem Kontakt ein Strom dieser Höhe auf eine Spannung von 1.500 Volt umgeschaltet, um den Verschleiß zu testen.
Ist das Leben eines Laststufenschalters hart! Er muss bei sengender Wüstenhitze ebenso zuverlässig arbeiten wie bei sibirischer Winterkälte. Selbst wenn der Blitz einschlägt, darf unsere Stromversorgung nicht unterbrochen werden. Neben den ganz alltäglichen Härten im Netzbetrieb gibt es noch zahlreiche Spezialanwendungen, die den Laststufenschalter besonders fordern. Dazu gehören beispielsweise die enormen Schaltzahlen bei einem Ofentransformator im Stahlwerk.
Als Hersteller für diese Komponenten hat MR also eine große Verantwortung. Dr. Thomas Strof, Leiter Erprobung Produktabsicherung bei MR, erklärt: „Wir müssen garantieren, dass unsere Laststufenschalter in jeder spezifischen Anwendung einen sicheren Betrieb ermöglichen.“ Seit 2008 steht ihm und seinem Team dafür ein weltweit einzigartiges Test-Center zur Verfügung. Es ist das Herzstück der Forschungs- und Entwicklungsabteilung und eine Art Folterkammer, in der die Experten die Laststufenschalter bis aufs Äußerste quälen. „Für Anwendungen im normalen Netzbetrieb müssen wir dabei natürlich anders testen als für einen Phasenschieber“, sagt Strof. Nur, wenn jeder Prototyp die speziell auf seine späteren Aufgaben abgestimmten Qualen übersteht, geht er auch in die Produktion.
Einzigartiges Folterzentrum
Das Ziel ist es, Normen wie IEC, IEEE oder JEC nicht nur zu erfüllen, sondern sie zu übertreffen. „Internationale Normen für Laststufenschalter verlangen 500.000 Schaltungen. Für unsere Vakuumschalter weisen wir 1,2 Millionen mechanische Schaltungen nach.“ Manchmal greifen Normen aber auch zu kurz oder klammern spezielle Anwendungsfälle aus. „Wir haben jahrzehntelange Erfahrungen im Feld und wissen auch bei Spezialfällen, welche Parameter zusätzlich getestet werden müssen, damit ein sicherer Betrieb möglich ist.“
Und dann sind da technologische Entwicklungen, für die es keine Norm gibt, weil sie einfach noch zu neu sind. „Diesen Fortschritt gestalten wir selbst aktiv mit. Aufgrund unserer Erfahrung und unserer Simulationsmodelle können wir Gefahren schon voraussehen und dann entsprechend prüfen“, erklärt Strof. Es gibt also viel zu tun. Das ganze Jahr über drangsalieren deshalb auf 4.800 Quadratmetern voll automatisierte Teststände die Schalter mit elektrischen, mechanischen oder klimatischen Extrembedingungen. Nirgendwo sonst auf der Welt kann das gesamte Spektrum der Belastungen so umfassend nachgebildet werden.
HOCHSPANNUNGSPRÜFUNG
Im Hochspannungslabor, einer Halle mit den Maßen 20 x 13,5 x 12 Meter, erzeugt ein Spannungsimpulsgenerator bis zu 1,8 Millionen Volt mit einer Anstiegszeit von lediglich einer Millionstelsekunde. So können die Laststufenschalter auf ihre Blitztauglichkeit geprüft werden. Da die Halle vollständig mit Metall umhüllt ist, damit kein Funksignal oder ähnliche Impulse von außen hineingeraten, werden hier auch die Teilentladungsprüfungen durchgeführt.
LEISTUNGSTESTS
Lastströme von 6.000 Ampere und Stufenspannungen von bis zu 5.000 Volt jagen die Ingenieure zur Prüfung der elektrischen Leistungsfähigkeit in die Stufenschalter. So qualifizieren sie Merkmale wie Kontaktverschleiß, Schaltgeschwindigkeit oder Lichtbogendauer.
TEMPERATURTESTS
In den zwei Temperatur-Prüfkammern wird der Einfluss von Kälte und Hitze auf unsere Produkte erprobt. Hier erzeugen wir Temperaturen von minus 70 Grad Celsius bis plus 130 Grad Celsius. Aber auch die Laststufenschalter selbst erzeugen Wärme. Dafür gibt es die Erwärmungsprüfungen. Laststrom führt zwingend zu einer Erhöhung der Temperatur im Stufenschalter, die jedoch bestimmte Grenzwerte nicht übersteigen darf. Wie ein Fieberthermometer, aber an mehreren Dutzend Stellen und unter Öl prüfen Thermoelemente daher diese Effekte.
KURZZEITSTROMPRÜFUNGEN
Um gegen einen Kurzschluss gefeit zu sein, muss ein Stufenschalter enorme physikalische Belastungen aushalten. Hierzu erzeugt die entsprechende Anlage Stromamplituden von bis zu 100.000 Ampere im Labor.
MECHANISCHE PRÜFUNGEN
Ein Stufenschalter besteht aus jeder Menge mechanischer Teile wie Getriebe, Gestänge oder Federn. Damit sie auch nach vielen Jahren noch zuverlässig ihren Dienst verrichten, werden harte Funktions- und Belastungstests durchgeführt und wo nötig durch Wiederholung auch noch statistisch abgesichert.
TROCKNUNGSTESTS
Transformatorisolierungen werden heutzutage per Vapour-Phase-Technik getrocknet. Dieses moderne Verfahren ist zwar sehr effektiv, aber auch physikalisch belastend. Um negative Effekte auszuschließen, wird dieser Trocknungsprozess im Labor nachgestellt.
Das gesamte Test-Center ist durchgängig mit modernster Leittechnik ausgerüstet. Sie steuert alle Vorgänge schnell, fehlerfrei und hoch automatisiert. Auftretende Störungen werden sofort angezeigt. Ein klimatisiertes Kalibrierlabor stellt die notwendige Genauigkeit der Prüfgeräte sicher. „Das Test-Center ist von der Deutschen Akkreditierungsstelle nach der Norm DIN EN ISO/IEC 17025 zertifiziert. Das bestätigt auch offiziell unsere extrem hohen Prüfstandards“, betont Strof.
