Reinhausen has an extensive portfolio of transformer service work to offer the US market. General Manager Bernhard Kurth explains in an interview how this is accomplished.
What is going on within the US energy sector at the moment?
The country is vast, spanning ten million square kilometers. As you can imagine, it is an enormous task to keep up the infrastructure. While there are major metropolitan areas on the east and west coasts, there are also huge stretches of land that are only sparsely populated. But power is needed everywhere.
The outdated technology in the primary substations is the main challenge to be faced. Here in the USA, we have some 200,000 power transformers with an average age of around 40 years. More than 2,000 new transformers are installed every year, but there is a lot of old equipment already in place. So a great deal of investment will be needed in the coming years.
How can Maschinenfabrik Reinhausen help to ease the situation in the United States?
On the one hand, we produce on-load tap-changers that address the specific requirements in the USA. But we also offer an extensive service portfolio including the modernization of transformers as well as the installation and testing of new ones. When a customer places an order for a new transformer, it is supplied by the manufacturer along with separate add-on parts.
This is where we come in! We take care of the entire installation process and integrate bushings, coolers, fans, and control boxes. This is what we call “dressing” the transformer. Finally, we take care of the oil processing and the vacuum filling of the transformer and then complete all necessary field tests. As you can see, we provide a full service so that the customer doesn’t have to worry about a thing.

What does the modernization process entail?
When we are tasked with taking care of modernization, we generally have to drain the transformer oil first. We can then proceed to complete several tasks, such as replacing the tap changer regardless of which manufacturer supplied it in the first place. We also install new bushings, regasket the transformer, replace radiators and fans, valves, indication instruments, and so on.
Once all of the modernization steps are complete, we fill the transformer back up with oil under vacuum. Some of our customers also want to digitalize their transformers so that they can keep an eye on the relevant data online. Unfortunately, this isn’t always an option– especially with older transformers. But we do try to offer this service where possible.
How do you know that it’s worth investing?
It really depends on the residual “transformer life.” Temperature degrades the paper insulation, which is the main indicator of residual transformer life. As long as the insulation is in good condition, modernization is a viable option to bring the transformer into a reliable condition for the next 20 — 30 years.
But of course it also depends on current market conditions for new transformers such as price and lead time. In general, modernization is attractive for medium and large power transformers.
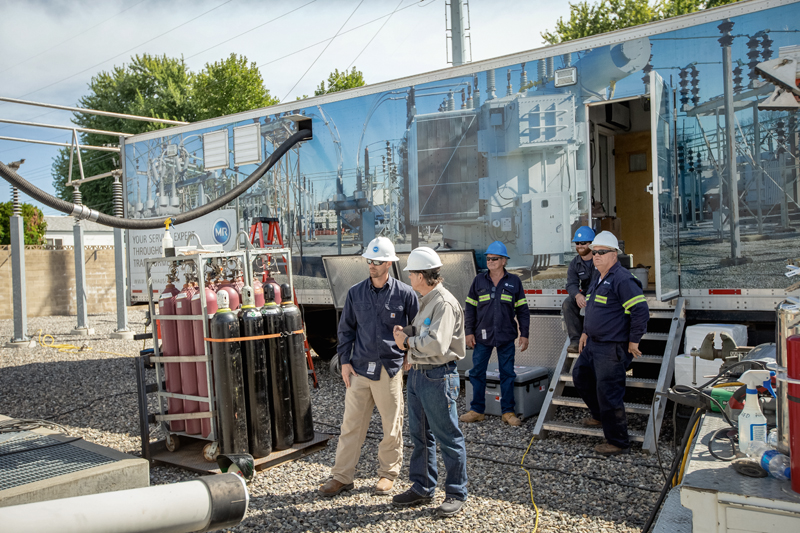
So what’s the point of modernizing?
The fact that you can wait for up to 24 months for a new transformer to be delivered is obviously an important factor. Modernization can be the much quicker option. Not to mention that modernization is often pushed forward as a way of guaranteeing reliability. For example, energy suppliers have to offer a certain level of dependability in line with their legal responsibilities and legal mandates.
Who are your customers?
Transformer manufacturers are, of course, one of our main customer groups when looking at new installations. Then we have energy suppliers, which include some major companies like Southern California Edison with some 15 million customers and Dominion Virginia Power with 7.5 million customers. They reach capacity limits when it comes to services like maintenance of their own transformers, so they use external providers like us to help them out.
“We have positioned our equipment strategically so that we are always as close as possible to our customers.”Bernhard Kurth, General Manager of Reinhausen Manufacturing Inc.
Finally, we also serve industrial customers. With the extremely high number of operations of their OLTCs, in some cases 100 to 1,000 times higher than for utilities, a more invasive inspection / maintenance need arises, which means entering the main tank. Here we offer a turn-key maintenance solution.
How is the service department set up in the USA?
Together with our sister companies ESS and ATSI we have a fleet made up of 24 service trucks and oil processing rigs. We use the latter to process thousands of liters of oil, which involves drying and degassing it, and then filling it back into the transformer under vacuum. They are a bit like dialysis machines used to clean blood. The fleet is based in Charlotte, from where they are typically dispatched. Two members of staff are typically assigned to each oil rig and it can take a few days for them to arrive at our customers’ premises.
150
The number of staff members employed by Reinhausen Manufacturing.
>100
The number of transformer work jobs the US team takes on in a year.
24
The number of service trucks ready and waiting to tackle maintenance tasks.
450
The number of customers Reinhausen serves across the USA, including energy suppliers, transformer manufacturers, and industrial companies.
Two extra employees are normally flown in, making up teams of four to work together on a job. With the acquisition of ESS and ATSI we have extended our reach even further geographically. Even though our sister companies are independent, we use them as subcontractors, calling on their staff and equipment when it makes sense to do so.
Generally speaking, our technicians are spread out across the USA, with our people based in Alabama, Missouri, Florida, North and South Carolina, and other states. They then drive or fly to where the work is.
What is the biggest challenge you face?
If you want to be competitive in offering this type of service across such a vast country, it’s important to position staff and equipment strategically so that nothing is ever too far away from the customers. That’s no mean feat here in the US.

But we promise a “nationwide” service so we go wherever there’s work for us to do! Of course, this can only work effectively if we stay on top of our rosters and coordinate schedules and work locations to perfection. In addition, we have to keep adding to our fleet of trucks and oil rigs.
What are your plans for the next few years?
We will continue to expand our network and equipment as demonstrated by our latest order for a new service truck and oil rig for the fleet. Furthermore, we are on the lookout for our next crew members. But we aren’t going to stop there – more orders will follow and we will need to add to our service team accordingly.
Reinhausen Heads West
Maschinenfabrik Reinhausen took the leap and headed across the pond to the land of opportunity back in 1987. We have continued to grow there since then and we now have four Reinhausen Manufacturing sites (see map). We have 150 employees working at these locations altogether. Plus, we have ESS in Phoenix (Arizona) and ATSI in Manchester (New Jersey), which have been part of the MR Group since 2016 and 2015 respectively. Humboldt, our oldest site, sticks to the more traditional side of the business, as this is where tap changers are produced and serviced.
Here we have centralized our Transformer Services Group and this is our home base, where we also perform maintenance on the service trucks, oil rigs and other equipment which we use to service our customers´ transformers. This type of service represents a growing market for us in the United States. We also have a sales force of Area Sales Managers who work from our four locations and from several home offices.
YOUR CONTACT
Do you have questions?
Bernhard Kurth is on hand to help you:
B.Kurth@us.reinhausen.com