The energy revolution and e‑mobility are driving the demand for copper to unforeseen levels. Mine operators are therefore expanding their production capacities and tapping new deposits. To do so, they require a stable supply of electricity and high power quality. René Rund explains how Reinhausen Power Quality can help.
Everything stops: the crushers that pulverize the blasted copper ore, the mills that then further process it, and also the conveyor systems that go on for kilometers—just to name the largest consumers. They are all electrically powered and the energy consumption is enormous. Depending on the size of the mine, a power requirement of up to 250 megawatts is not unusual. And it’s constant, seven days a week, around the clock.
In other words, the same electricity demand as a large city …
Exactly. Ensuring this supply is anything but simple, since deposits are usually in remote areas. In Peru, for example, we have a customer with a mine in the Andes at an altitude of over 4,000 meters, hundreds of kilometers from the nearest grid node.
This means that the power supply is dependent on one line. There is nothing like this in the tightly meshed grids of Europe. But you don’t even need a power outage to bring the machinery to a stop. Today, even a short voltage drop or overvoltage, which could be caused by lightning or certain switching operations in the grid, is enough.
Why is that the case?
Because modern drives are much more sensitive than they were 20 years ago. This affects mills in particular. It’s hard to believe when you see the machines—they are powerful giants with diameters of up to thirteen meters that can grind hundreds of tons at once. But the technology is vulnerable due to frequency-regulated drives, which facilitate precise control of the speed and torque.
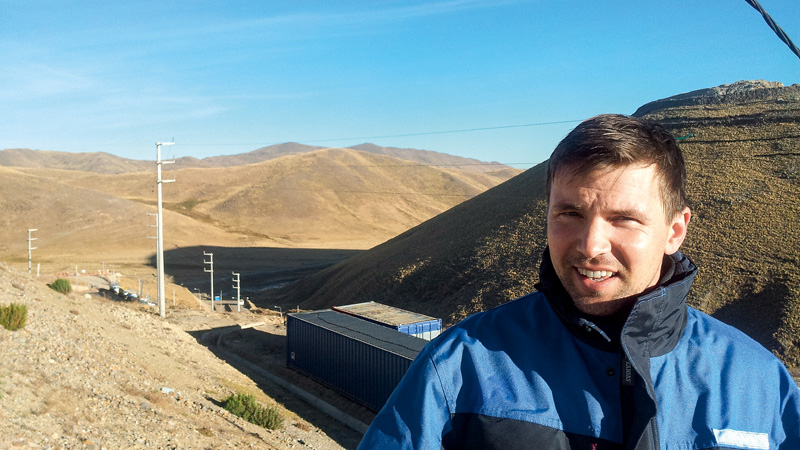
While this makes the machines significantly more efficient, they switch off if the voltage leaves the defined range. Where most deposits are found, such as in South America or Africa, the grids are generally very unstable—meaning that voltage fluctuations occur more often there. But that’s just the half of it. The machines themselves also have repercussions on the grid.
You mean the reactive power?
es, that too, reactive power flows overload the lines. In this way, this problem is not new. But with modern machines and their frequency-controlled drives, harmonics also arise that have a negative effect on the power quality. These grid impurities can also interfere with other consumers.

Therefore, grid operators set limit values, which mines and other large consumers have to comply with. If the limit values are exceeded, this can become really expensive. It can result in fines or even disconnection. But the mine operators also have an interest in eliminating harmonics, for a different reason: they can interfere with their own technology. If sensors or measurement technology fail, production stops.
Which solutions does Reinhausen Power Quality offer to overcome this undesirable grid feedback?
In a nutshell: compensation systems for reactive power and filter circuit systems for harmonics. But there isn’t just a single solution. Every mine is different, both with regard to the machine fleet and the topographical factors. There is therefore usually only one of each of our systems in the world. But our GRIDCON® series gives us a trusted modular system which we can tap into.
“Thanks to the GRIDCON® range, mine operators can improve their power quality and also utilize the available infrastructure more flexibly.”
In general, there is a clear trend toward dynamic compensation systems that can optimize load flows with power electronics almost in real time. This helps mine operators avoid transmission losses due to excessive reactive power and can thus also lower their energy costs. It is also possible to get more out of transformers and even connect additional drives since reactive power is offset on the process rail and does not go through the transformer. Mine operators can thus improve their power quality and also utilize the available infrastructure more flexibly.
And what about voltage fluctuations in the grids?
There is a specified voltage range in which the grid operator can allow the voltage to fluctuate. If this range is violated, our systems are also able to bring the voltage back to this range almost in real time. In turn, this then ensures stable production.
How long does such a system last?
We get this question frequently. 15 to 20 years. This always depends on the individual demand and how well the systems are maintained.
Are these dynamic systems also suitable for other industries?
Yes. The application is not limited copper mines; the systems can be used for mining as a whole as well as in other industries in which powerful consumers are connected to the grid. For example, electric arc furnaces in steelworks.
REINHAUSEN INSIDE
Reinhausen Power Quality offers custom solutions for the elimination of harmonics, reactive power compensation and voltage stabilization for all voltage levels. The experts are involved from the consultation phase, through the design stage, and even up to system setup. The training of employees can also be taken on if desired.
Solutions from the GRIDCON® series are available for the design of the filter circuit and compensation systems. GRIDCON® SVC, for example, is a system that reduces harmonics and improves the power factor. The GRIDCON® STATCOM system improves grid and voltage stability
YOUR CONTACT
René Rund, Senior Sales Manager at Reinhausen Power Quality
R.Rund@reinhausen.com