How the MSENSE® BM online monitoring system monitors bushings and the HiRES Locator identifies breakdowns in cable systems.
Check.
Bushing monitoring
Bushings are among the most sensitive components in transformers. Not only do they have to withstand several hundred thousand volts, they must also be able to support high thermal and mechanical loads. That’s why around 17% of major transformer failures are attributed to defective bushings. Likewise, such defects are also the main cause of transformer fires and explosions. Nevertheless, these can be avoided with an early warning system and timely replacement. For this purpose, Reinhausen has developed the MSENSE® BM online monitoring system, with which the condition of bushings can be continuously monitored. If the system detects a fault, an alarm is triggered, allowing the operator to intervene before a failure occurs.
To do this, the new monitoring system uses two key metrics – capacity and dissipation factor – which provide information on the condition of the insulation. A deviation of the bushing values in one phase (C1 or tan δ ) from the original values indicates that the condition of the insulation has changed and the user is notified using a two-stage limit-value system (warning and alarm).The process for analyzing the measurement data is complex. An algorithm developed by Reinhausen known as the double-reference method (2/3 reference method) eliminates the reliance on network imbalances and temperature fluctuations and therefore enables reliable and unambiguous condition assessment. Transformers that are already in operation can also be retrofitted with the MSENSE® BM online monitoring system.
YOUR CONTACT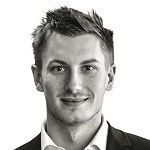
Want to know more about the new MSENSE® BM system?
Tobias Gruber is here to help:
t.gruber@reinhausen.com
Detect.
HiRES Locator
Where is the fault? Searching for breakdowns in miles of medium-voltage and high-voltage cabling is a little bit like looking for a needle in a haystack. Previously, a fault could only be pinpointed offline after a malfunction had occurred. The measurement needed would then be complex and time-consuming, and often additional investigation was needed before the fault could be localized. However, the experts at HIGHVOLT have now developed a new measuring device called the HiRES Locator, which makes fault localization quick, easy, and cost-effective. This is good news not only for grid operators and energy providers, who are required to monitor cabling systems of ever greater complexity, but also for cable manufacturers, who can integrate the HiRES Locator into their testing procedures for the purposes of quality assurance.
The HiRES Locator works in the following way: A digital recorder is connected to the cable during active operation and localizes a breakdown immediately while it’s occurring, so the fault is localized with the system still online, not after the fact. The measurement is based on the impulse reflection method, also known as TDR (time-domain reflectometry). Previously, measurement technicians using this method would generate an artificial break ‑down signal – an electrical impulse which would propagate through the conductor in wave form. If the wave encounters a material fault, it is reflected back. The location of the breakdown is then calculated from the time difference between the sent and received signal. The HiRES Locator can now determine this live and in real time.
Your Contact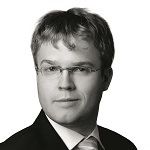
Want to know more about the HiRES Locator?
Tobias Mießler is here to help:
miessler@highvolt.de